履きやすさへのこだわり 職⼈が語るものづくり
「履きやすさ」を実現する工程を見てみる。
見た目に軽くなる素材加工
サンダルは足裏を支える台と甲を押えるベルトでできている。いたってシンプルだ。
デザイン部門の高橋は、だからこそ見た目が重要になると言う。
「重量をいちばん感じるのはアウトソールの見た目です。ゴム底は重そうに見えますね。このように、素材感が見た目の『重い/軽い』に影響するのです」。
そこで工夫する。
高橋は、使用する樹脂の量を減らすために中を蜂の巣状にしたソールを開発し、物理的な軽さを実現した。
一般的にはクレープソールやウレタンソールという、軽くて弾力性があり履きやすいアウトソールがよく使われる。
しかし時間が経つと劣化するし、硬化や加水分解により割れることもある。だからゴムを使うのだ。しかも軽くした。
「デザインに欠かせない素材なら、その素材を活かしつつ、履いてみると軽く、履きやすく感じさせるようにします」。
ファッションと履きやすさを両立させるための開発が「履きやすさ」を支えている。
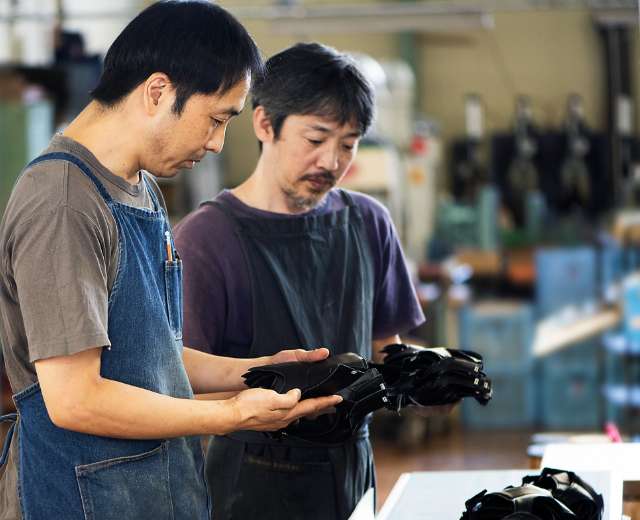
部門間の調整が
より良いラストを作る
「デザイナーに提案すると『ダメ』と言われ、デザイナーの意を汲んで工場に持っていくと今度は『それじゃ困る』と言われる。双方を尊重しながら調整し、型を仕上げる。そこが技術部門の役割です」と技術部の内山は言う。
型紙の貼りしろが小さかったり組み方に無理があったら、設計を変更するようにデザイナーに頼む。工数が多くかかると感じれば簡単に作れる方法を製造部門に提案する。
「サンダルを前から見ると履き口が鯉の口のようにグニャっとしていることがあります」と内山は指摘する。
町中を歩いていても、そういうサンダルがあるとついに目がいってしまうという。「これは吊り込むときの位置決めが間違っているから生じる問題です。角度や位置が合っていればこうはなりません」と内山は解説する。
足入れを確認していないラストだと、後で問題が生じるので肉付けの調整が必要になる。そういう時は自ら手を動かしてラストを補正することもある。
サンダルのどの部分がどの工程のどの機械で組み立てれるか、ラストにぴったり合わせるとはどういうことなのかがわかれば調整できると内山は言う。
ただし、「ぱっとわかるようになるまでには10年くらいはかかります」と内山は語った。
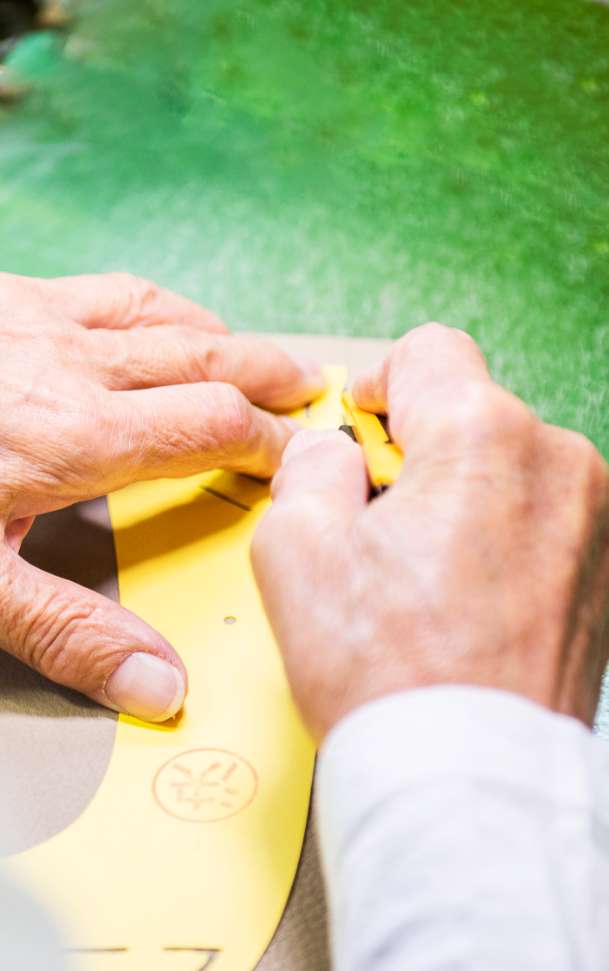
気持ちよい吊り込みが決め手
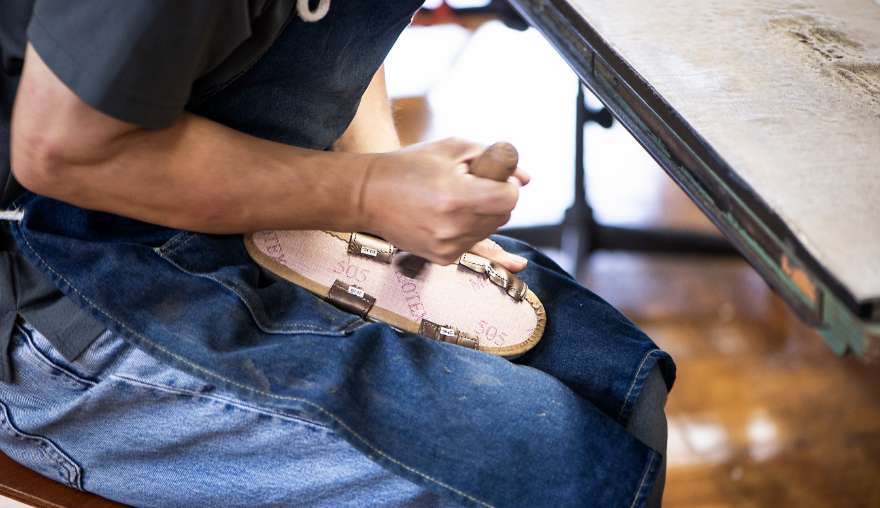
では、良いラストさえあれば、履きやすいサンダルができるのか。
ことはそう簡単ではない。サンダルだからこその難しさがある。靴とは違って、サンダルの履き口は浅く肉抜きされているものが多い。デザインによってはセンターが明確でごまかしがきかない。
製造部門の池谷は「ラストの丸みに合わせて、きつすぎず緩すぎずインソールとアッパーをラストに気持ちよく合わせて吊り込むことが大事。これが履きやすさを決めます」と言う。
吊り込みとは、中底に仮止めしたラストにアッパーを被せ、被せたアッパーの周辺を引っ張って中底とアッパーを接着剤で固定する工程。
ここで靴の形が決まる。サンダルは通常の靴よりも細い紐のパーツも多く、手仕事で吊り込む技術が必要だ。
1日に300~400足を製造すると「指が痛い」と作業者が言い出すが、「妥協せずに激励し続けるのが工場長の仕事です」と池谷は平然と言う。
ものづくりのこだわり
駿河塗下駄作りを祖とするダイマツが、今に継承するこだわりとは何か。
3人のレジェンドに聞いた。
ダイマツ・ものづくりのレジェンドたち
- 企画・デザイン部門 高橋和夫氏
- 1967年入社 研修後デザイン部門に配属。オリジナルブランドを数多く手掛ける
- 技術部門 内山隆資氏
- 1967年入社 海外工場立ち上げや技術指導を経て技術部門に。約10ブランドのグレーディングを行った
- 製造部門 池谷鑛一氏
- 1978年入社 静岡県内の工場にてあらゆる製品の製造を担う。手がけたブランドは50を超える
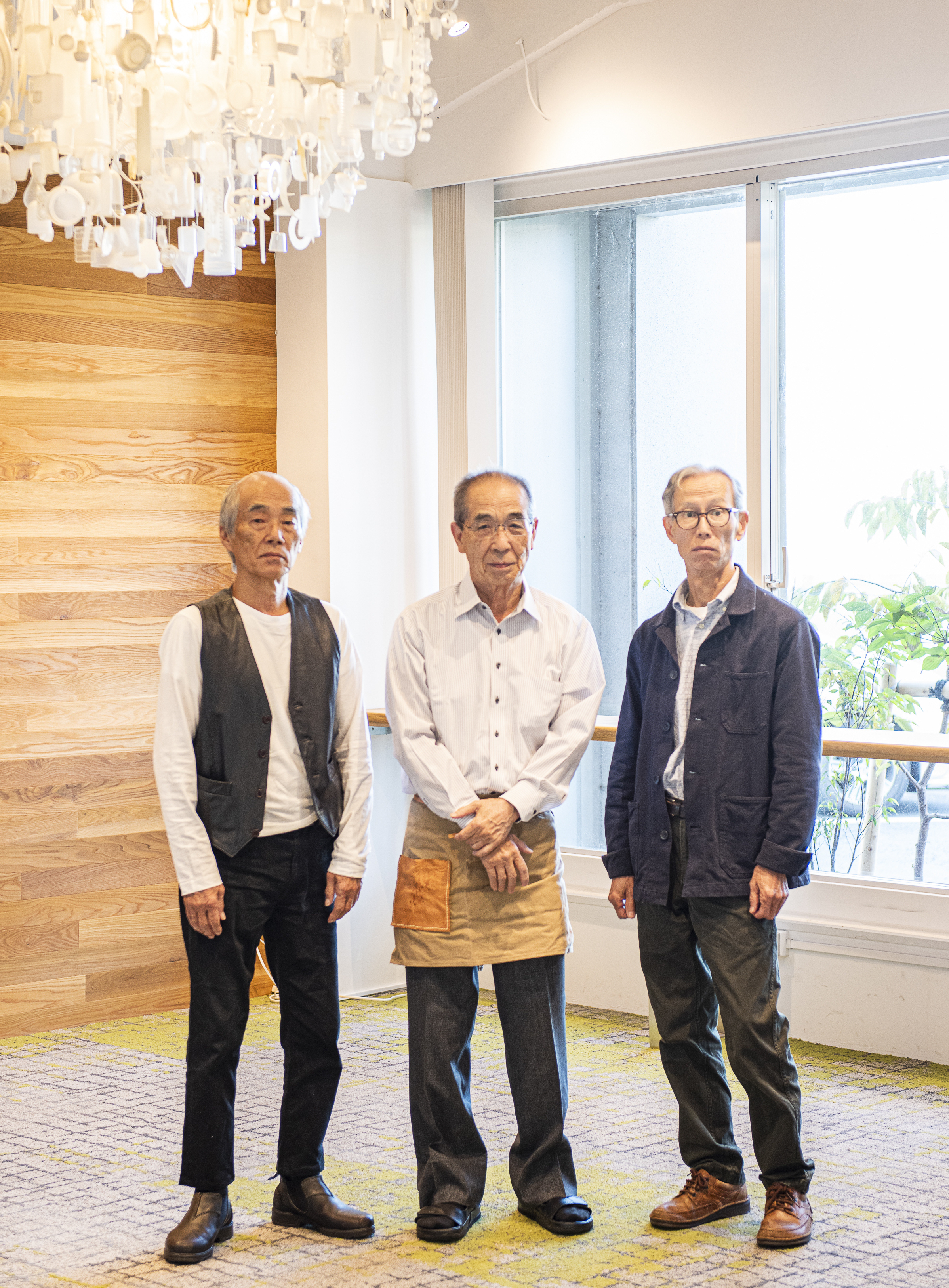
左から高橋、内山、池谷