The Joy of Making Footwear Daimatu’s Manufacturing
Renowned artist Taro Okamoto once remarked, “Footwear has walked alongside human history, treading upon the earth, and
supporting life—a familiar companion.” In these words, one finds not only the boldness of an artist but also the
strength, warmth, and joy inherent in footwear.
What joy is derived from the continuous work of crafting familiar companions?
Customers readily acknowledge the enhancements
‘Crafted by Mr.Takahashi from the design department, the lady’s footwear brand Croissant was inspired by international
designs and quickly became a hit with its single-strap style. However, around 5-6 years after its launch, complaints
surfaced regarding colour fading.
Due to the high volume of shipments, immediate improvements were necessary. “Initially, I tried applying adhesive to the
back of the leather to prevent colour fading, but it didn’t work. Eventually, I decided to stop using single-piece
uppers and instead incorporate spandex in the area where the foot’s arch touches,” Mr.Takahashi explains.
The real challenge began there. I experimented with various thicknesses of sponge to be applied behind the spandex,
incrementally changing it by millimetres. In order to maintain the shape, I also had to adjust the thickness of the
leather.
“At first, I used a thick 2.5mm single piece of leather, but eventually, we reduced it to 1-1.2mm,” Mr.Takahashi
reveals.
Leather is a difficult material, prone to colour variations and challenging in terms of texture. Each time it didn’t
match the specified colour or exhibited too much colour variation, I had to start over. If the leather was too stiff, it
wouldn’t fit the design. I negotiated with material suppliers numerous times. Finally, the improved product was
completed and shipped out with confidence.
Upon hearing feedback, like ‘no colour fading’ and ‘more comfortable than before,’ I breathed a sigh of relief.
“I was delighted to see my designed sandals being well-received. Seeing people wearing them brings me the greatest joy,” Mr. Takahashi says with a beaming smile.
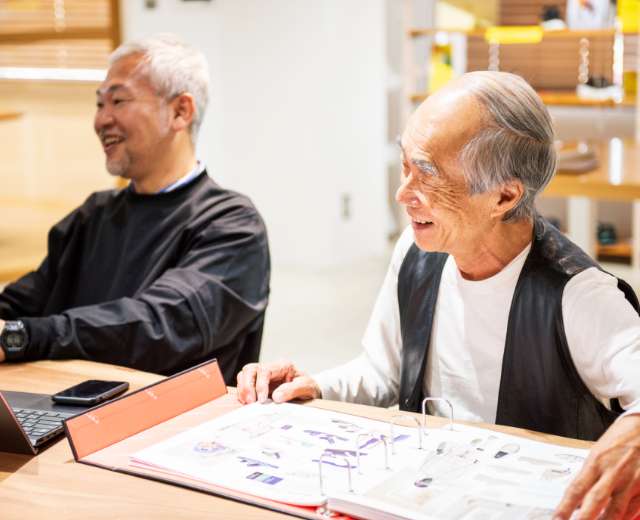
The feeling of achievement in surmounting a challenge
The initial task assigned to Mr.Uchiyama from the technical department was to establish a factory for a joint venture in Indonesia. Upon joining the company, it wasn’t the era of computer-controlled machines as it is today. Confronting a foreign country with distinct language, culture, and climate posed significant challenges. “Every day brought its share of troubles, requiring manual adjustments. It was a busy 4 years and 7 months,” recalls Mr.Uchiyama.
However, these diverse experiences equipped him with comprehensive knowledge of the entire manufacturing process. Upon returning to Japan, he transitioned to the technical department. “I received extensive technical guidance from senior colleagues in the design and manufacturing departments,” reflects Mr.Uchiyama.
Consequently, he became proficient in pattern adjustments, grading, sewing, and lasting. “There were no computers back then; everything was done manually,” he chuckles, yet recognizing the invaluable nature of his experience. His confidence stems from the ability to adapt to any situation—a cornerstone of his approach.
He consistently resolves challenges and incorporates them into the factory’s workflow. The gratification of overcoming intricate adjustments and completing the mould is a source of deep personal fulfilment for him.
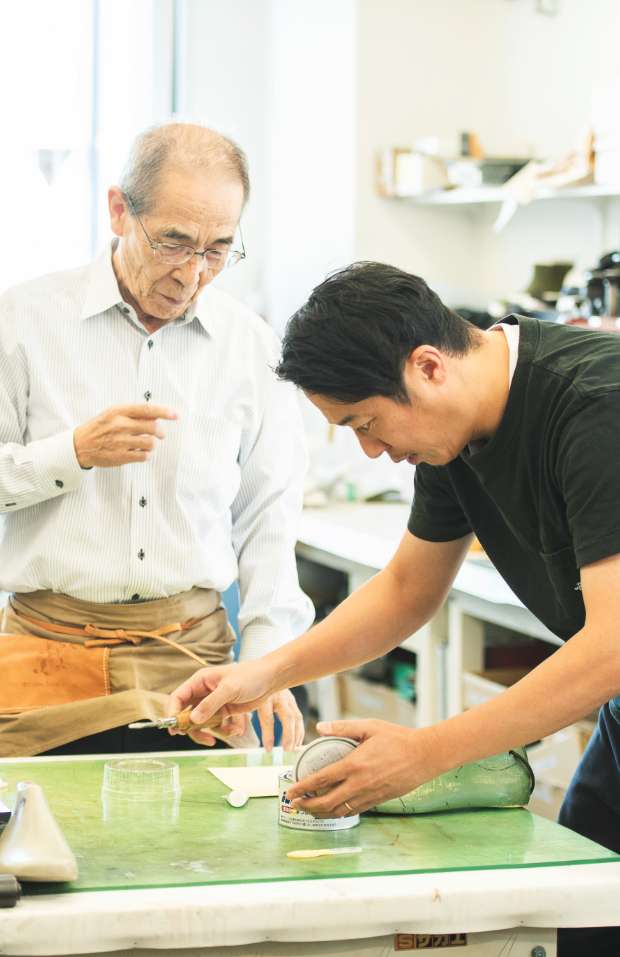
At its essence lies a sense of purpose.
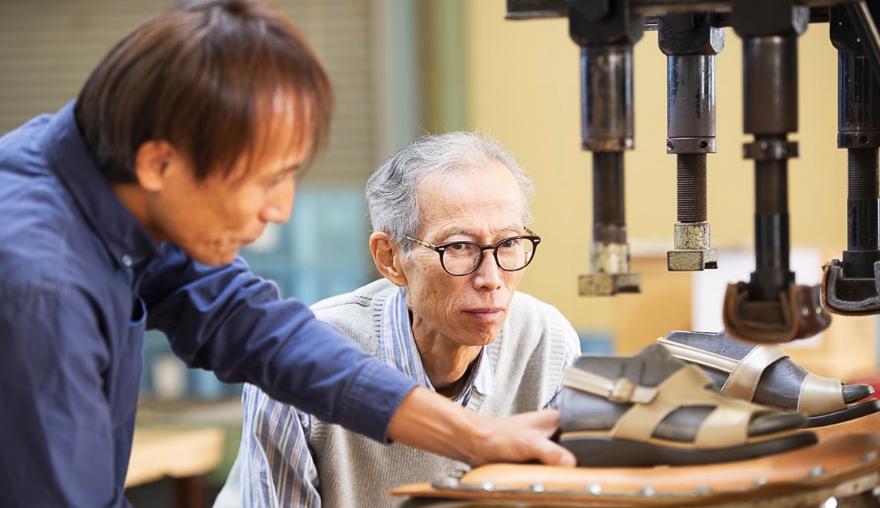
“On the manufacturing floor, doing things properly is a given and there exists a deep-seated sense of duty in doing so”
says Mr.Ikegaya, who served as the head of the manufacturing floor.
He finds himself consistently impressed by the advanced technology of globally renowned brands and the facilities adept
at mass production. “Yet,” he continues, “through meticulous consideration and validation of production methods, one can
truly appreciate the superiority of Japanese materials and manufacturing techniques.”
For instance, Japanese adhesives and their application methods stand out significantly. While abroad, there appears to be a limited selection of adhesive types, Daimatu actively engages with adhesive manufacturers to exchange information and select the most suitable adhesive for each product.
Navigating cultural disparities proves both intriguing and challenging. “When working with materials boasting unique patterns, we encountered issues aligning the mould, the cutting method, and the appearance of patterns and colour on the fabric. Designs featuring differing patterns on the left and right sides are not widely embraced in Japan. Therefore, we meticulously crafted each piece by pairing similar patterned materials together,” explains Mr.Ikegaya. Despite encountering obstacles, they consistently overcome them with accumulated experience and wisdom.
Mr.Ikegaya proudly asserts, “It’s a capability unique to Daimatu.”
Daimatu, rooted in the tradition of crafting Suruga lacquered geta, remains committed to its passion to this day. We caught up with three legends to hear about their dedication first-hand.
Daimatu's Legendary Artisans
- Planning and Design Department Takahashi Kazuo
- After joining us in 1967 as part of the design department, Mr.Takahashi has played an active role in the planning and development of numerous products for our original brands.
- Technical Department Uchiyama Takashi
- After joining us in 1967, Mr.Uchiyama initially contributed to establishing overseas factories and providing technical guidance before transitioning to the technical department. There, he oversees the technical checks and grading for all our products.
- Manufacturing Department Ikegaya Kouichi
- After joining us in 1978, Mr.Ikegaya worked at our manufacturing plants in Shizuoka Prefecture, overseeing the production of various products. He has contributed to over 50 brands during his tenure.
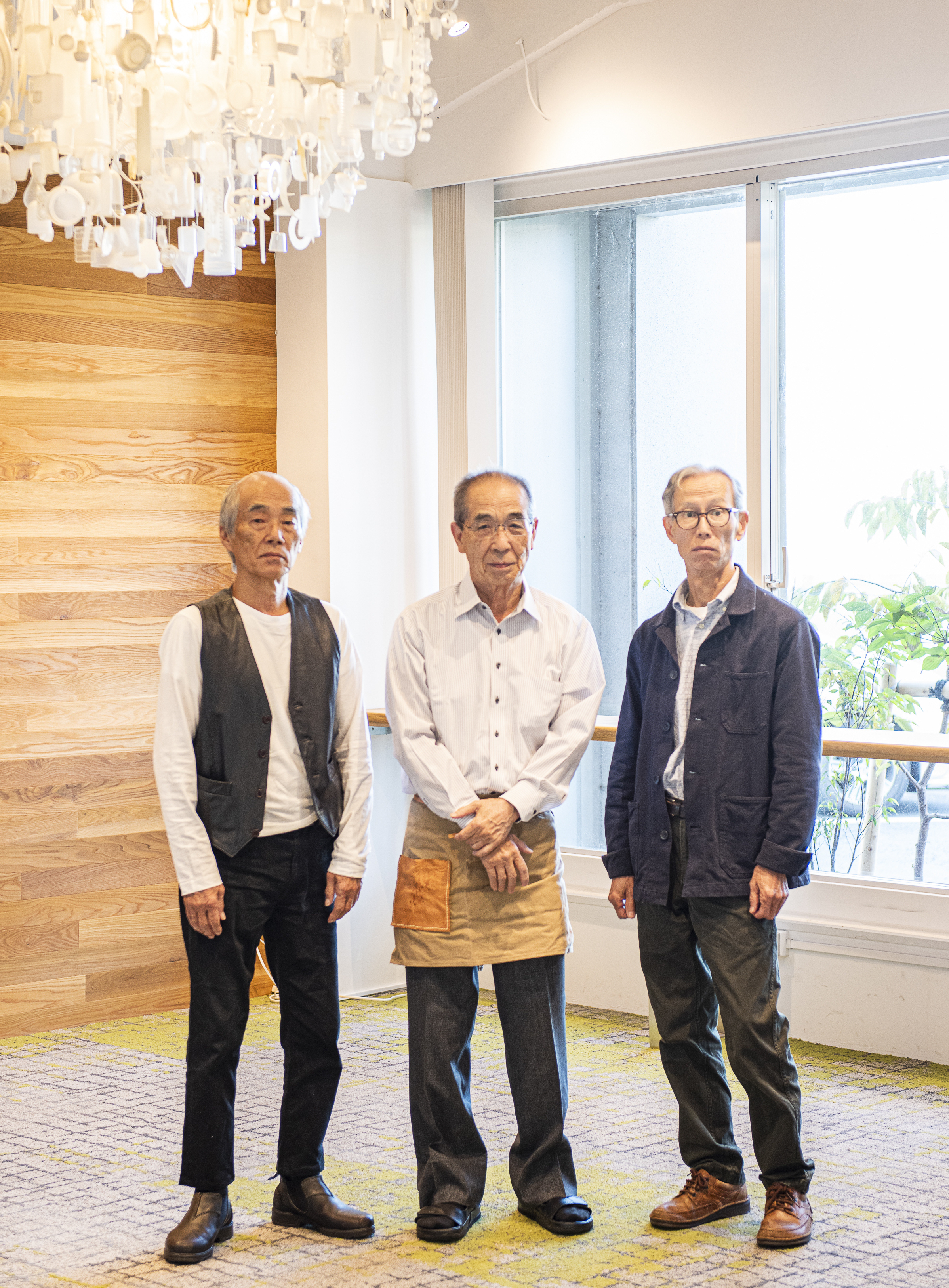
From left to right, Mr.Takahashi, Mr.Uchiyama, Mr.Ikegaya